In the chemical industry, habitual processes require sealing elements for materials with high chemical resistance. For transferring very aggressive or corrosive chemical fluids that are clean or with particles and have high viscosities, along with high temperatures and pressures, the mechanical seal materials and the type of assembly must be correctly defined: single, double, external, or in accordance with API plans.
Furthermore, the applications require sealing systems that guarantee safety, preventing the leakage of corrosive or flammable products that could enter the atmosphere. In this sector ATEX certification is often required, to ensure equipment's safety when working in explosive environments.
All the above gives rise to extremely demanding requirements for the mechanical seals and for the auxiliary elements supplied with them: LTS or LQT reservoirs, or elements such as cyclones.
Not only is it necessary to pay attention to the design of the mechanical seal, but also to consider the materials used to make its components: sintered silicon carbide contact surfaces (Q1), fluorinated elastomeric seals (FKM) or high resistance alloy springs (Hastelloy C) are an indispensable requirement.
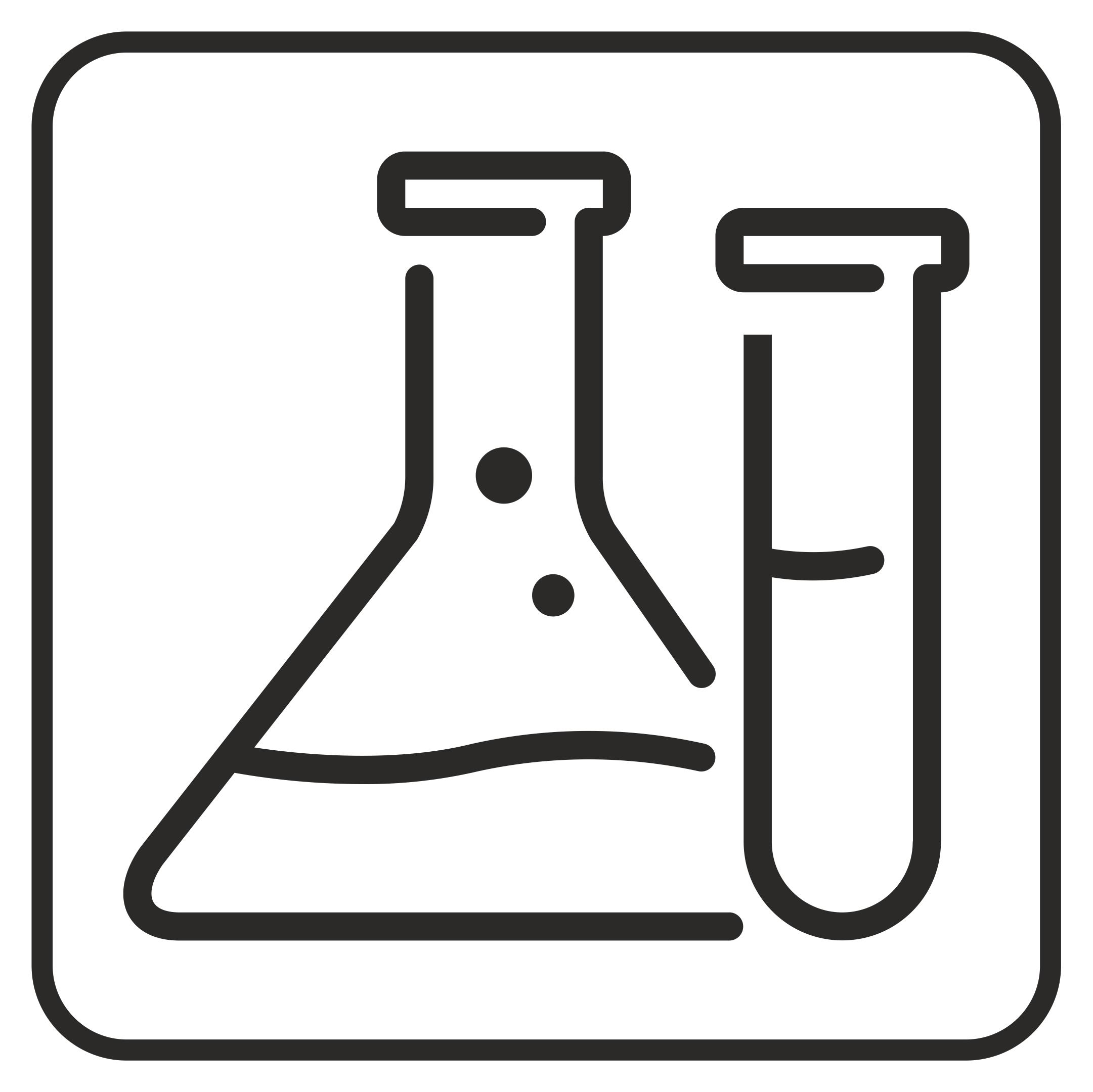